Introduction
Diesel generators play a crucial role in providing backup power in various industries, commercial establishments, and residential settings. These generators are relied upon to ensure continuous operations during power outages or in areas where grid power is unreliable. However, like any mechanical system, diesel generators are prone to faults and failures that can lead to costly downtime and maintenance expenses. To address this challenge, fault detection systems have been developed to monitor the health of diesel generators and detect potential issues before they escalate into major problems. In this article, we will explore the importance of fault detection in diesel generators, the common types of faults that can occur, and the technologies and techniques used for fault detection.
Importance of Fault Detection in Diesel Generators
The uninterrupted operation of diesel generators is critical for many applications, including hospitals, data centers, telecommunications facilities, and manufacturing plants. Any unexpected downtime can result in financial losses, compromised safety, and damage to equipment. Fault detection systems are designed to proactively identify issues within the generator system, allowing for timely intervention and preventive maintenance. By detecting faults early, operators can avoid costly repairs, minimize downtime, and ensure the reliability of their backup power source.
Common Types of Faults in Diesel Generators
Diesel generators are complex systems that consist of various components such as the engine, alternator, cooling system, fuel system, and control panel. Faults can arise in any of these components, leading to performance degradation or complete system failure. Some of the common types of faults that can occur in diesel generators include:
1. Fuel System Issues: Problems with the fuel supply, such as fuel contamination, air in the fuel lines, or fuel pump malfunctions, can result in poor engine performance and reduced power output.
2. Cooling System Failures: Issues with the cooling system, such as coolant leaks, clogged radiators, or malfunctioning thermostats, can cause the engine to overheat and lead to catastrophic engine failure.
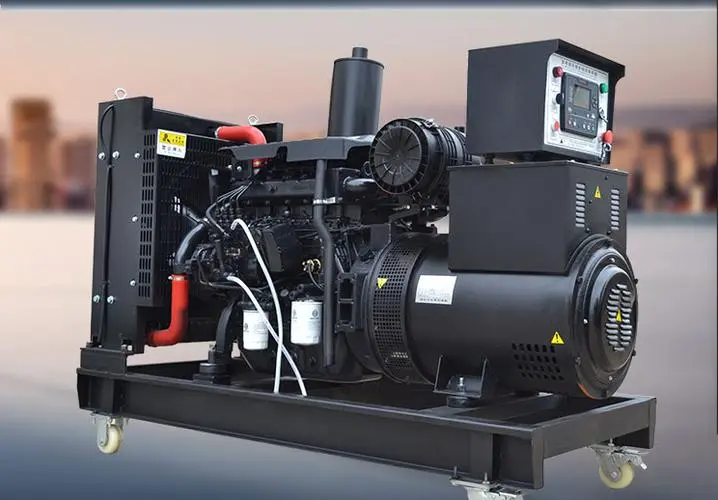
3. Battery and Starter Motor Problems: Faulty batteries or starter motors can prevent the generator from starting or cause starting delays, affecting the generator's ability to provide backup power when needed.
4. Lubrication System Failures: Inadequate lubrication or oil leaks can cause excessive wear on engine components, leading to premature failure and reduced engine lifespan.
5. Electrical System Faults: Problems with the alternator, voltage regulator, or electrical connections can result in voltage fluctuations, electrical surges, or power quality issues that can damage connected equipment.
Technologies and Techniques for Fault Detection in Diesel Generators
To effectively monitor the health of diesel generators and detect faults, a variety of technologies and techniques are employed. These include:
1. Condition Monitoring Systems: Condition monitoring systems use sensors to collect data on various parameters such as temperature, vibration, oil pressure, and fuel consumption. By analyzing this data, operators can identify trends and anomalies that may indicate potential faults.
2. Remote Monitoring and Diagnostics: Remote monitoring systems enable operators to track the performance of diesel generators in real-time from a centralized location. Any deviations from normal operating conditions can trigger alerts for immediate action.
3. Predictive Maintenance: Predictive maintenance techniques involve the use of advanced analytics and machine learning algorithms to predict when a component is likely to fail based on historical data and performance trends. This proactive approach helps prevent unexpected downtime and costly repairs.
4. On-Board Diagnostics: Modern diesel generators are equipped with on-board diagnostic systems that continuously monitor key parameters and self-diagnose potential faults. These systems provide valuable insights into the health of the generator and enable early detection of issues.
5. 500kw diesel generator for events and AI: Data analytics tools and artificial intelligence algorithms can analyze large volumes of data collected from diesel generators to identify patterns, correlations, and anomalies that may indicate potential faults. These technologies enable operators to make informed decisions and take preventive actions to maintain the reliability of their generators.
Conclusion
Fault detection systems play a crucial role in ensuring the reliable operation of diesel generators in various applications. By proactively monitoring the health of generator components, detecting faults early, and implementing preventive maintenance measures, operators can minimize downtime, reduce maintenance costs, and optimize the performance of their backup power systems. The integration of advanced technologies such as condition monitoring, remote diagnostics, predictive maintenance, on-board diagnostics, and data analytics is essential for enhancing the reliability and efficiency of diesel generators. In an increasingly interconnected world where uninterrupted power supply is a necessity, fault detection systems are indispensable tools for maintaining the resilience of critical infrastructure.